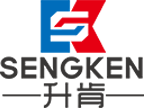
XIAMEN SENGKEN INDUSTRY&TRADE CO.,LTD.
OEM Metal And Plastic CNC Milled Turned Parts CNC Prototype Service
Part Name :
OEM Metal And Plastic CNC Milled Turned Parts CNC Prototype ServicePart No :
GHD000010Part Size :
Many sizes for choice,see the photos/Accept CustimizationPart Plastic material :
PP,PVC,PE,ABS,POM etc.Part Weight :
as per customer's drawingPart Color :
White/Orange/Grey/Black/OEM as per your requestSurface Treatment :
Matte, Common polishing, Mirror polishing, Texture, Plating, Power Coating (Painting), Laser Engraving, Brushing, Marbling, Printing etc.Tonnage of injection molding machine :
88T~1650TCavity Number :
Customized according to demand/1*1,1*2,1*4,1*6,1*8,1*12,1*16,1*24,1*32,1*48 etcRunner :
Hot Runner / Cold RunnerPlastic Molding Type :
InjectionDrawing Format :
.stp / .step / .igs /.stl /.dwg / .pdfItem:OEM Metal And Plastic CNC Milled Turned Parts CNC Prototype Service
Material: ABS, PC/ABS, PP, PC, POM(Acetal/Delrin), Nylon 6, Nylon 6/6, PA 12, HDPE, LDPE, PS(HIPS), PMMA(Acrylic), SAN/AS, ASA, PVC, UPVC, TPE, TPR, PU, TPU, PET, PEI(Ultem), PSU, PPSU, PPE/PS, PTFE(Teflon), GPPS, PPS, PPO, PES, CA, etc.
Certificate: IATF 16949:2016 / ISO 9001:2015 / ISO 45001:2018 / ISO 14001:2015 /REACH/ROHS/MSDS/LFGB
Drawing Format: .stp / .step / .igs /.stl /.dwg / .pdf
Parameters: Inch, centimeter, millimeter, etc.
Surface Treatment: Matte, Common polishing, Mirror polishing, Texture, Plating, Power Coating (Painting), Laser Engraving, Brushing, Marbling, Printing etc.
Mold Material: S136H, 718H, NAK80, P20, H13, etc.
Mold Life-cycle: 100,000-500,000 shots.
Product Photo:
Many kinds of raw material are frequently used, such as ABS, PC/ABS, PP, PC, POM, Nylon (PA6, PA66, PA12), PE, PS, PMMA(Acrylic), SAN/AS, ASA, PET, PVC, TPE, TPR, TPU, TPV. We can produce plastic products in some special materials, such as PBT, PEI (Ultem), PEEK, PSU, PPSU, PPE, PPE/PS, PTFE (Teflon), GPPS, PPS, PPO, PES, PPA, CA, DMC, PF, etc.
We can also add some additives according to the functional requirements of the project to improve the performance of the product, such as Reinforcing Agents, Flame Retardants, Fillers, Functional additives, Elastomer toughening agents, Weathering agents, Reflective agents, etc...
Mould Design Process:
Step 1: Analyze the product drawings
Step 2:Create the Design for Manufacturability (DFM) report
Step 3: Make the mould flow analysis
Step 4: Design tooling drawings
Step 5: Mould making