Item: Furniture Round Plastic Leg Chair Sofa Bed Table Plastic Feet
Material: ABS, PC/ABS, PP, PC, POM(Acetal/Delrin), Nylon 6, Nylon 6/6, PA 12, HDPE, LDPE, PS(HIPS), PMMA(Acrylic), SAN/AS, ASA, PVC, UPVC, TPE, TPR, PU, TPU, PET, PEI(Ultem), PSU, PPSU, PPE/PS, PTFE(Teflon), GPPS, PPS, PPO, PES, CA, etc.
Certificate: IATF 16949:2016 / ISO 9001:2015 / ISO 45001:2018 / ISO 14001:2015 /REACH/ROHS/MSDS/LFGB
Drawing Format: .stp / .step / .igs /.stl /.dwg / .pdf
Parameters: Inch, centimeter, millimeter, etc.
Surface Treatment: Matte, Common polishing, Mirror polishing, Texture, Plating, Power Coating (Painting), Laser Engraving, Brushing, Marbling, Printing etc.
Mold Material: S136H, 718H, NAK80, P20, H13, etc.
Mold Life-cycle: 100,000-500,000 shots.
Product Photos:
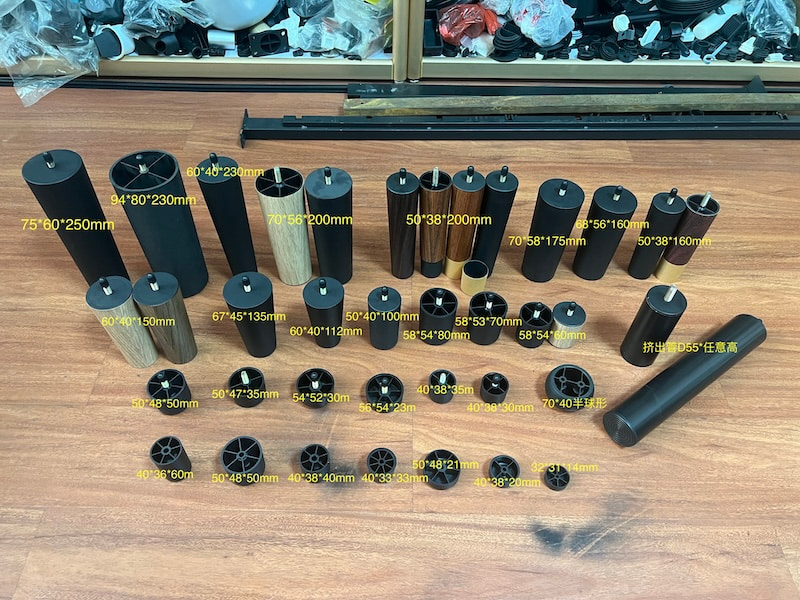
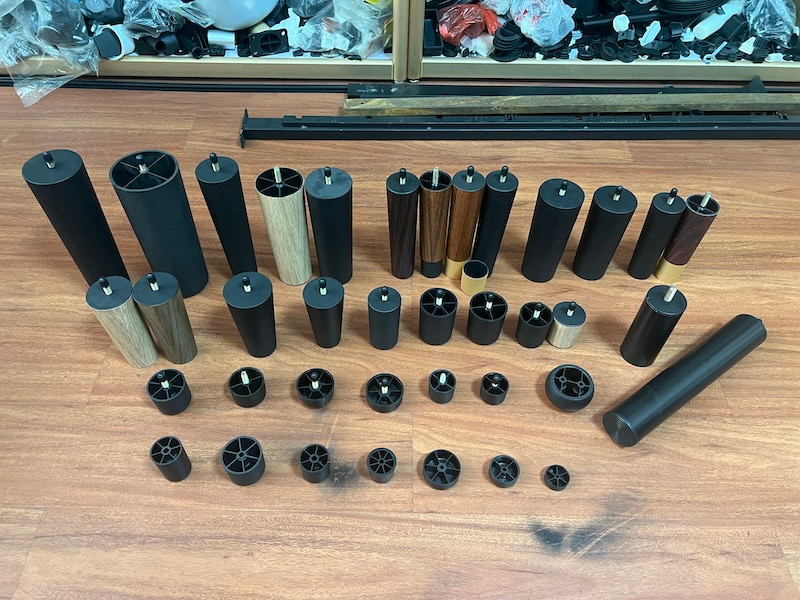
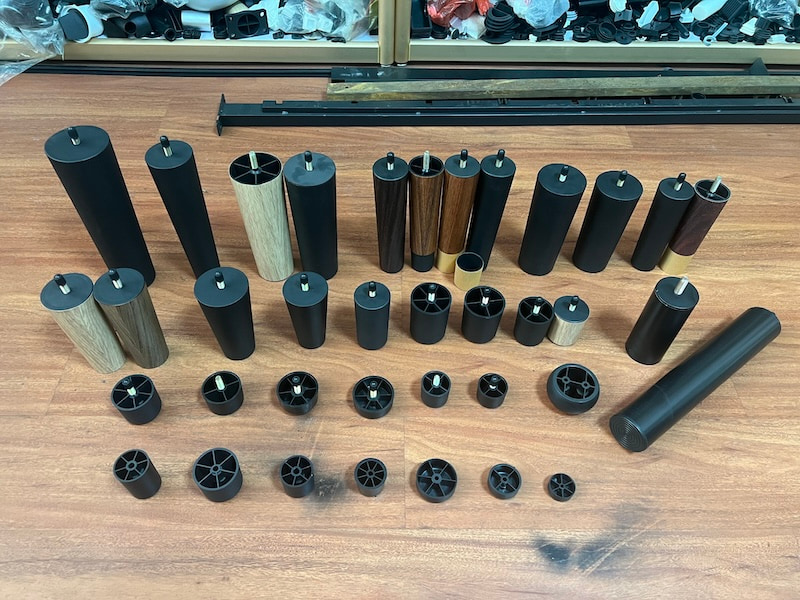
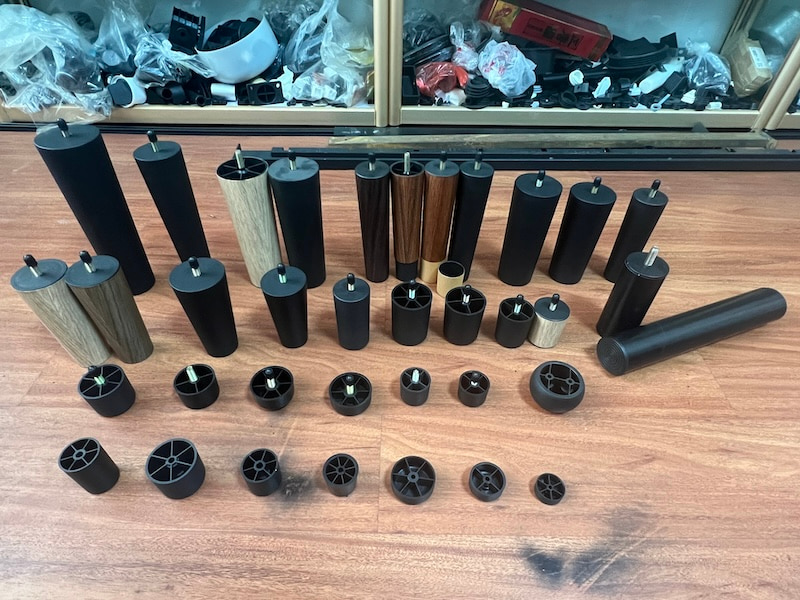
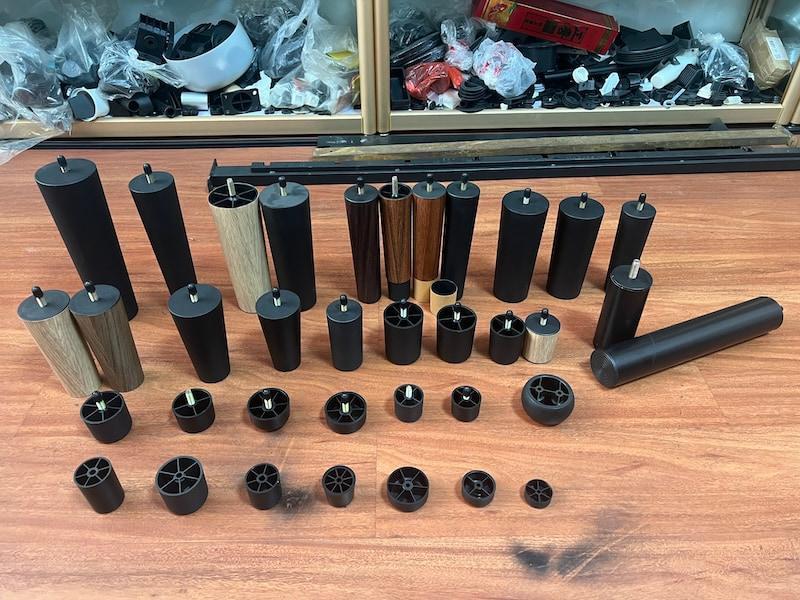
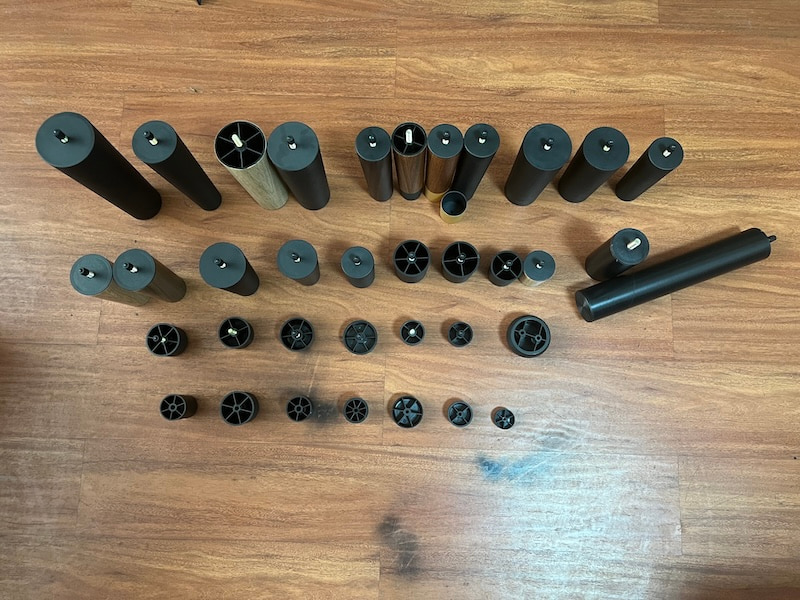
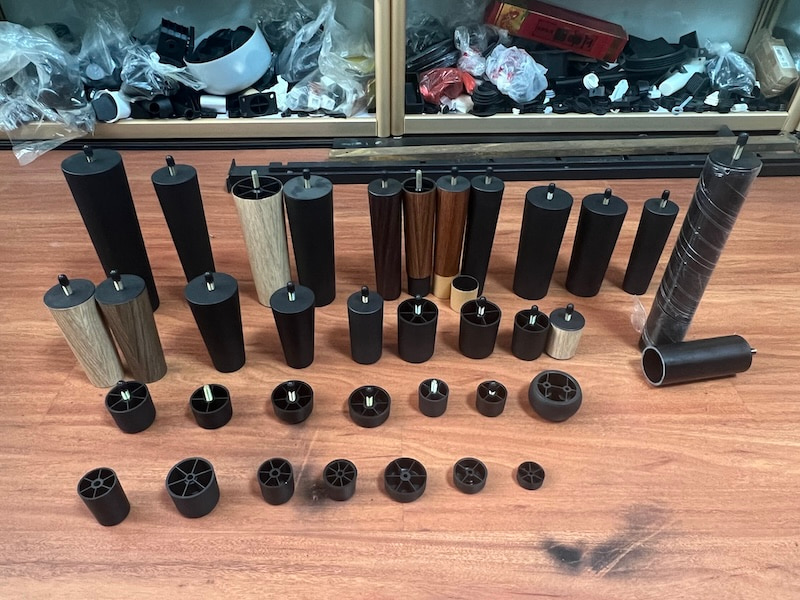
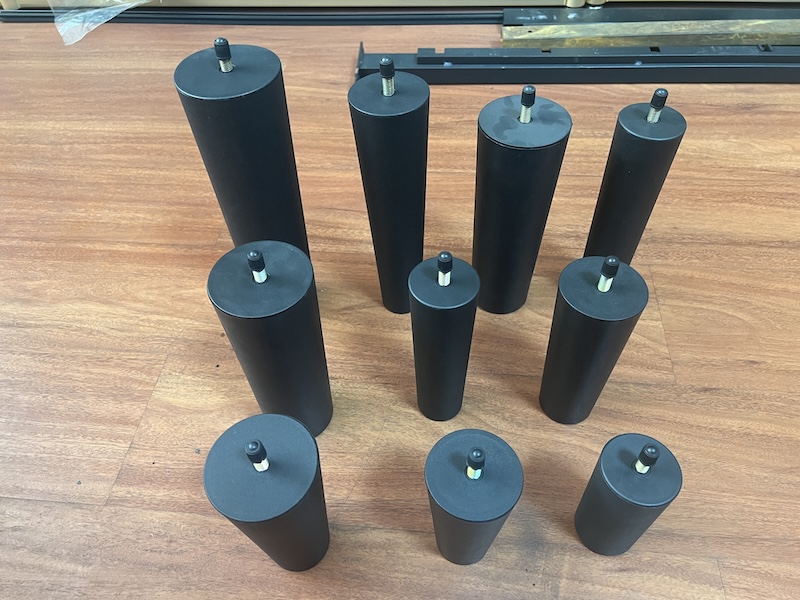
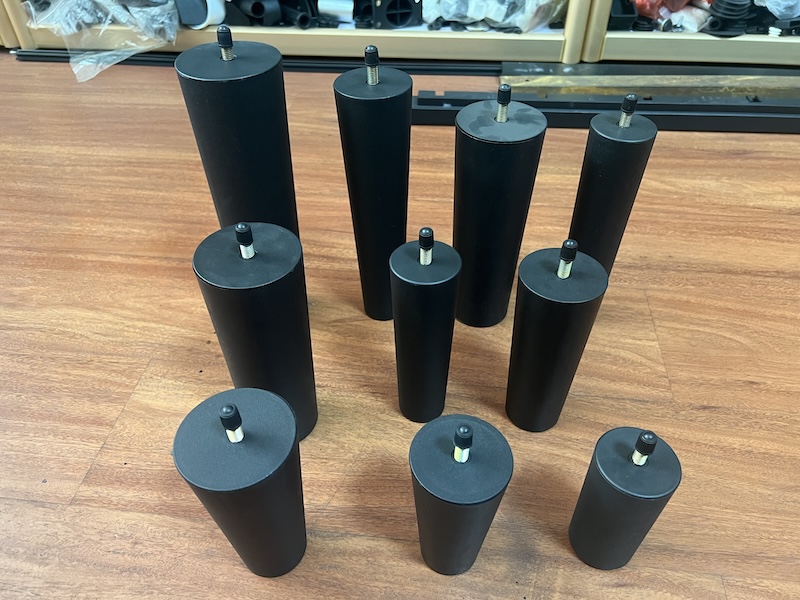
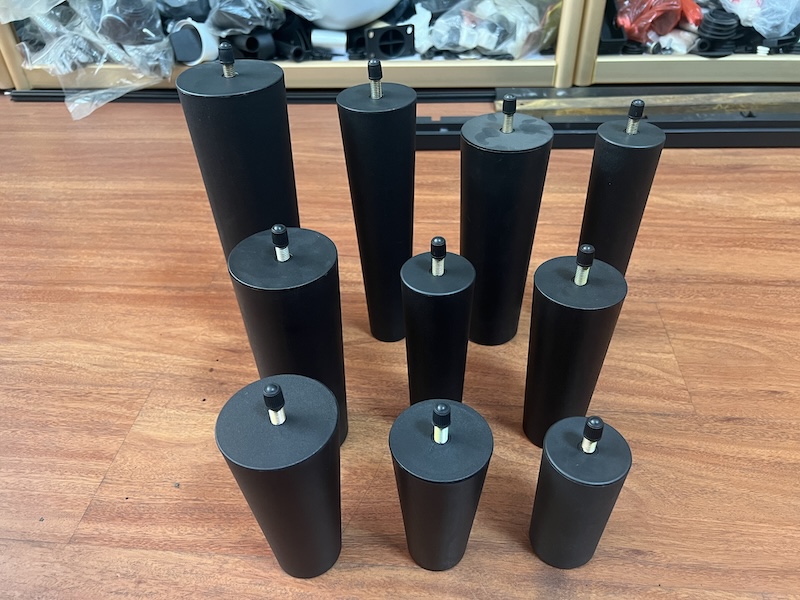
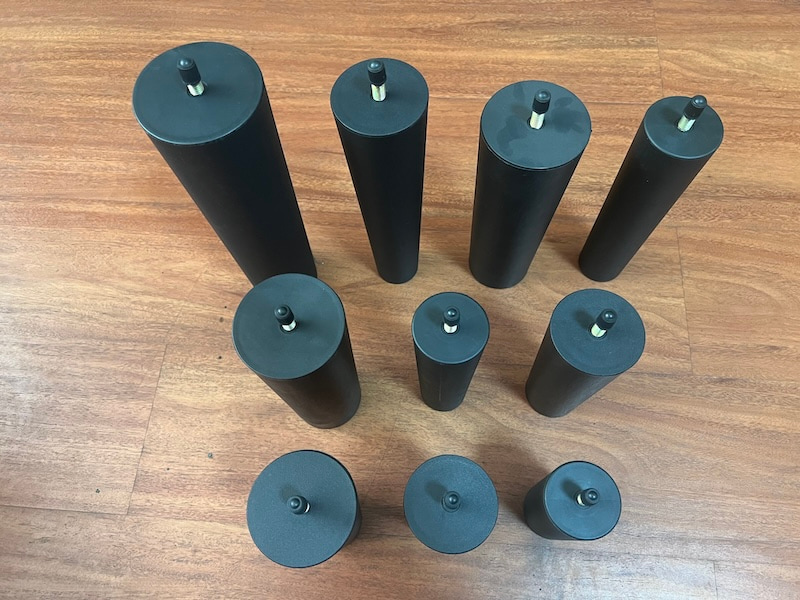
Many kinds of raw material are frequently used, such as ABS, PC/ABS, PP, PC, POM, Nylon (PA6, PA66, PA12), PE, PS, PMMA(Acrylic), SAN/AS, ASA, PET, PVC, TPE, TPR, TPU, TPV. We can produce plastic products in some special materials, such as PBT, PEI (Ultem), PEEK, PSU, PPSU, PPE, PPE/PS, PTFE (Teflon), GPPS, PPS, PPO, PES, PPA, CA, DMC, PF, etc.
We can also add some additives according to the functional requirements of the project to improve the performance of the product, such as Reinforcing Agents, Flame Retardants, Fillers, Functional additives, Elastomer toughening agents, Weathering agents, Reflective agents, etc...
There are some plastic parts for reference:
Company Profile
Plastic injection molding is the preferred process for manufacturing plastic parts, as it is ideal for producing high volumes of low-cost plastic parts with high tolerance precision, repeatability and little to no finishing required.
We have 37 sets injection molding machines, includes the multi-color injection molding machines, the biggest one is 1650T. Our capability for Plastic part is up to 1500mm.
Supply Ability
Workflow after customer order is placed:
Mould Design Process:
Step 1: Analyze the product drawings
Step 2:Create the Design for Manufacturability (DFM) report
Step 3: Make the mould flow analysis
Step 4: Design tooling drawings
Step 5: Mould making
Once the mould making is finished, we’ll make several pieces of pre-production samples for test, if the dimensions are correct, then we will send the samples to customers for final confirmation. If the test failed, we will modify the mould or adjust the molding parameter to make new samples, and test it again. Once the samples are approval by customers, we will purchase the raw material and making quality inspection. Then mixing material, molding and trimming, we will make many times of inspection during the production. Finally we will arrange the assembly and packing. After whole order is ready, we will send the packing list to customer to arrange the shipment.
We can also provide double-color and triple-color injection molding
Double-color injection molding and triple-color injection molding process can make the appearance of the product more beautiful, and easy to change the color without painting, but the cost is expensive and the technical requirements are high.
Related products:
And we have10,000 level dust-free production workshop for biomedical products.
Highly Welcome Custom Your Own Designs !!!
Why choose us
We seriously take care of the quality control from IQC to OQC, throughout each step of the production.
Let us show you our quality control:
For raw materials, we’ll do the IQC in time. All materials are procured only from the verified suppliers, who have implemented and maintain certified quality management systems in their plants.
With full certificates, such as RoHs, Reach, MSDS, FDA, LFGB, UL, EN549, BPA free, EN71, and so on;
For pre-production samples, we'll provide several pieces to our clients for assembly and function testing. We will seal the samples in time once they're approval.
For Bulk Production, we'll do the IPQCS & PQC (Multiple Sampling Inspection) during production and we'll do the FQC (Sampling
Inspection) after deburr or breaking sharp edges.In order to timely find problems, solve problems, reduce defective products,
reduce manufacturing costs.
After packing and assembling, we'll do the OQC (Sampling Inspection) to make sure the final goods are qualified.